Interbloc Mould Tracking System
Upcycling Surplus Concrete with High-Tech Product Design Expertise
Each year NZ generates approximately 300,000 tonnes of surplus concrete destined for landfill – that’s enough concrete to build 7 Sky Towers! Concrete trucks usually carry a little more than is required for a pour, to ensure there is always enough concrete to finish the job.
Envirocon’s solution is to ‘up cycle’ this excess wet concrete to make precast Interblocs. Interblocs are 1 ton pre-cast concrete blocks, used for retaining walls and other construction applications. By using surplus concrete, Envirocon’s Interblocs achieve a 97% reduction in embodied carbon compared to fresh concrete.
Envirocon faced a significant challenge with manufacturing the Interblocs: they needed to match an unpredictable supply of surplus concrete (which had a limited time window before it hardened) with the availability of empty block moulds across multiple sites. This was a slow, manual process.
The Goal: Real-Time Visibility and Optimized Asset Utilization
Envirocon needed real-time visibility of the status of all block moulds at every site. This would allow optimal routing of surplus concrete to maximize asset utilization and reduce environmental impact.
Additionally, Envirocon wanted to improve tracking of concrete in the moulds, and the blocks they were turned into. This would allow them to better monitor the process, ensuring that all blocks met required standards.
Collaborating with Globex for a Smart Solution
Envirocon envisaged installing a physical tracker on each mould, and setting up a database for tracking their status and location. But they had to keep their focus on core business operations, and did not have product development experience internally. Therefore, Envirocon partnered with Globex to design and implement the solution.
A wireless tag was preferred over manual entry or barcode scanning, to make the system quick and easy for staff to use. NFC technology was chosen for its low cost, simplicity, and lack of battery or power needs.
Another key requirement was for the tracker to be robust enough to withstand the tough industrial environment, where the steel moulds were moved around with large forklifts, and subjected to significant forces during transport and demoulding. The final design needed to:
attach securely to steel moulds
protect the electronics from shock and vibration
endure exposure to sun, frost, and high-pressure washdowns
perform for many years in these harsh conditions
Globex explored various concepts, materials, shapes, and attachment methods with Envirocon, before committing to a final design which features a low-profile housing engineered to withstand impact. The bright green colour aligns with Envirocon’s branding, and contrasts with the steel moulds for easy identification. The NFC tag is shielded from shock and vibration.
Envirocon preferred to manufacture locally, so Globex chose a New Zealand plastics company to create the tooling and mould the parts. Globex managed the sourcing of components from various local and international suppliers - where feasible, off-the-shelf components were used to reduce capital costs and development time. Globex assembled the initial production batches in their prototyping lab. Finally, Globex developed a system to help Envirocon consistently and accurately attach the tracker tags to the moulds, ensuring they worked reliably.
Exceeding expectations and reducing waste
The implemented system, which includes trackers, a smartphone app, and a backend database, provides real-time visualization of all concrete moulds. Key benefits include:
Faster and more accurate tracking of moulds
Optimized asset utilization, reducing excess capital tied up in underused moulds across multiple locations
Efficient rerouting of trucks carrying surplus concrete, reducing transport costs
Enhanced quality assurance through accurate tracking of mould curing times
High operational reliability in a harsh industrial environment
A Sustainable Future for Envirocon
Envirocon is now better equipped to expand operations and recover a larger portion of New Zealand’s surplus concrete, which would otherwise go to waste. Envirocon can also more efficiently expand their range of precast concrete blocks, allowing their low-carbon solution to replace a wider range of environmentally damaging alternatives.
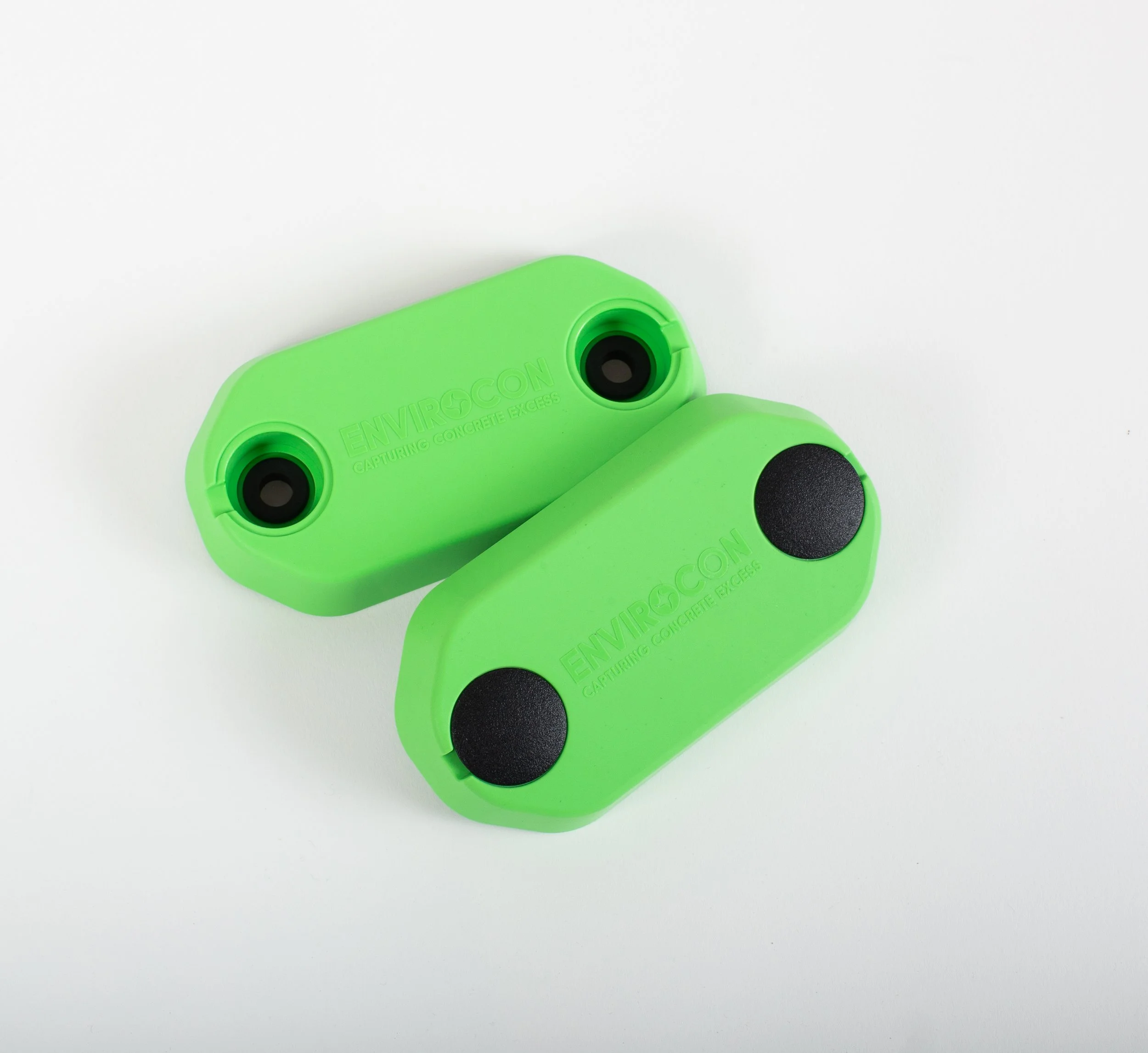

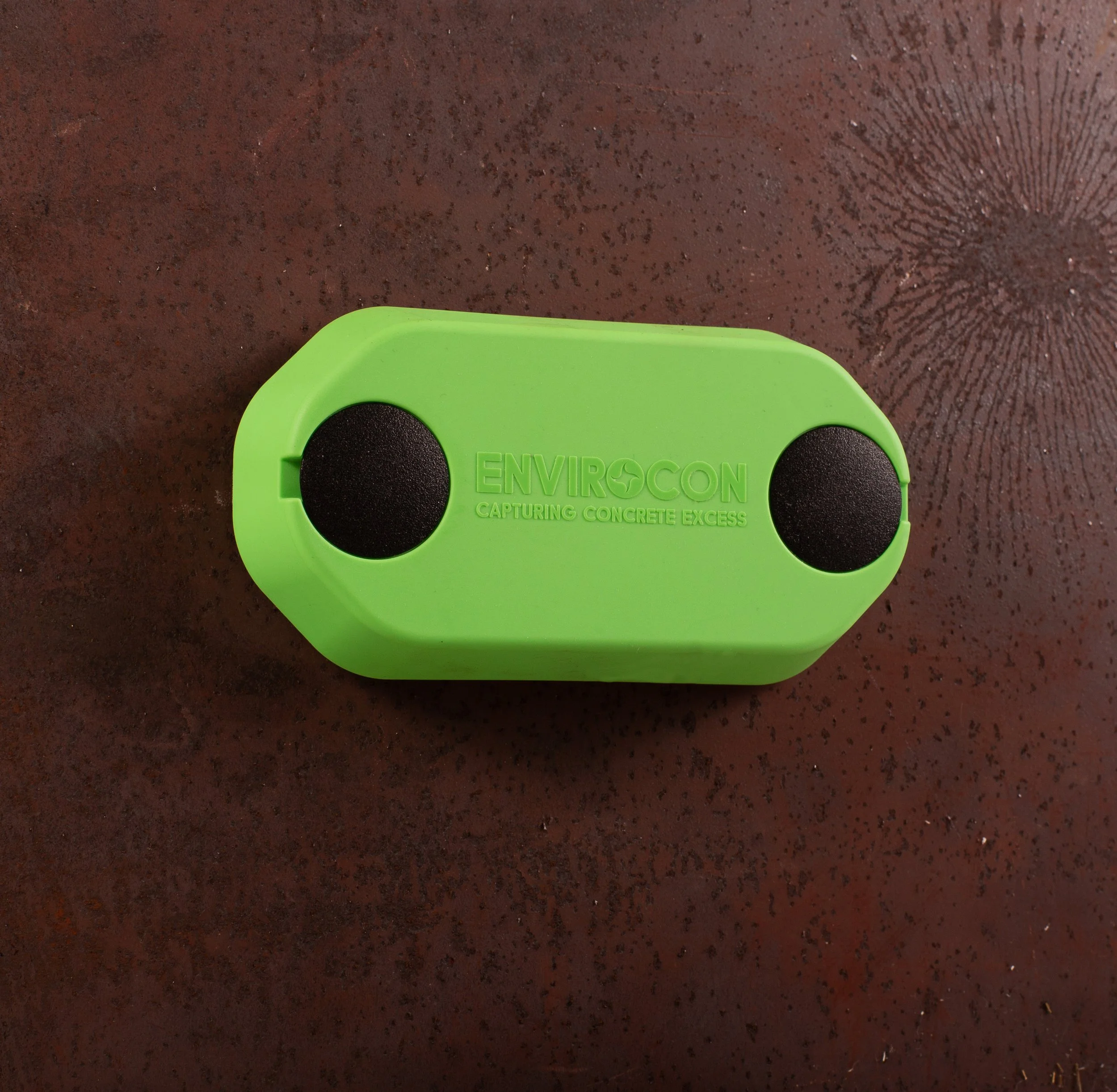
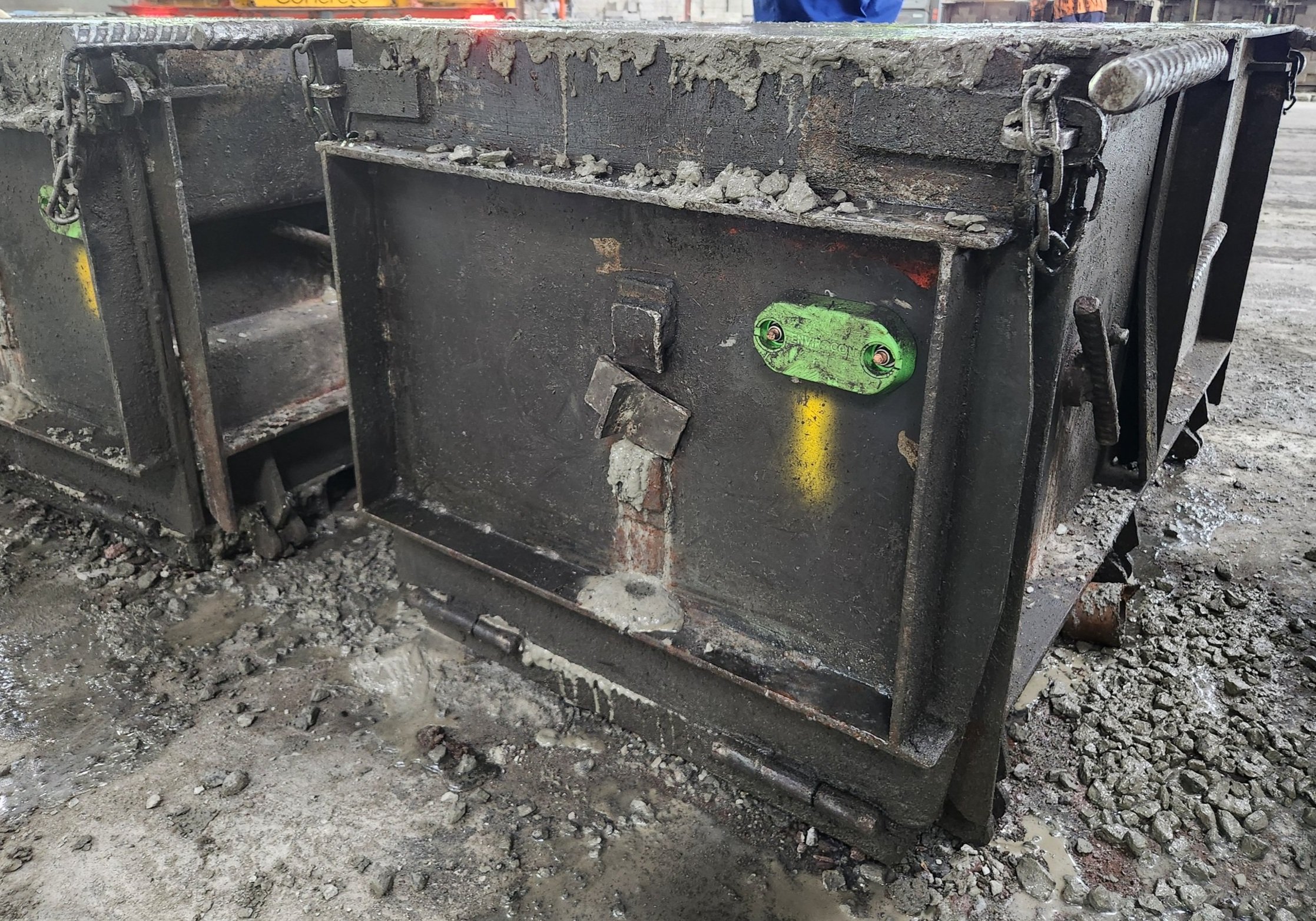
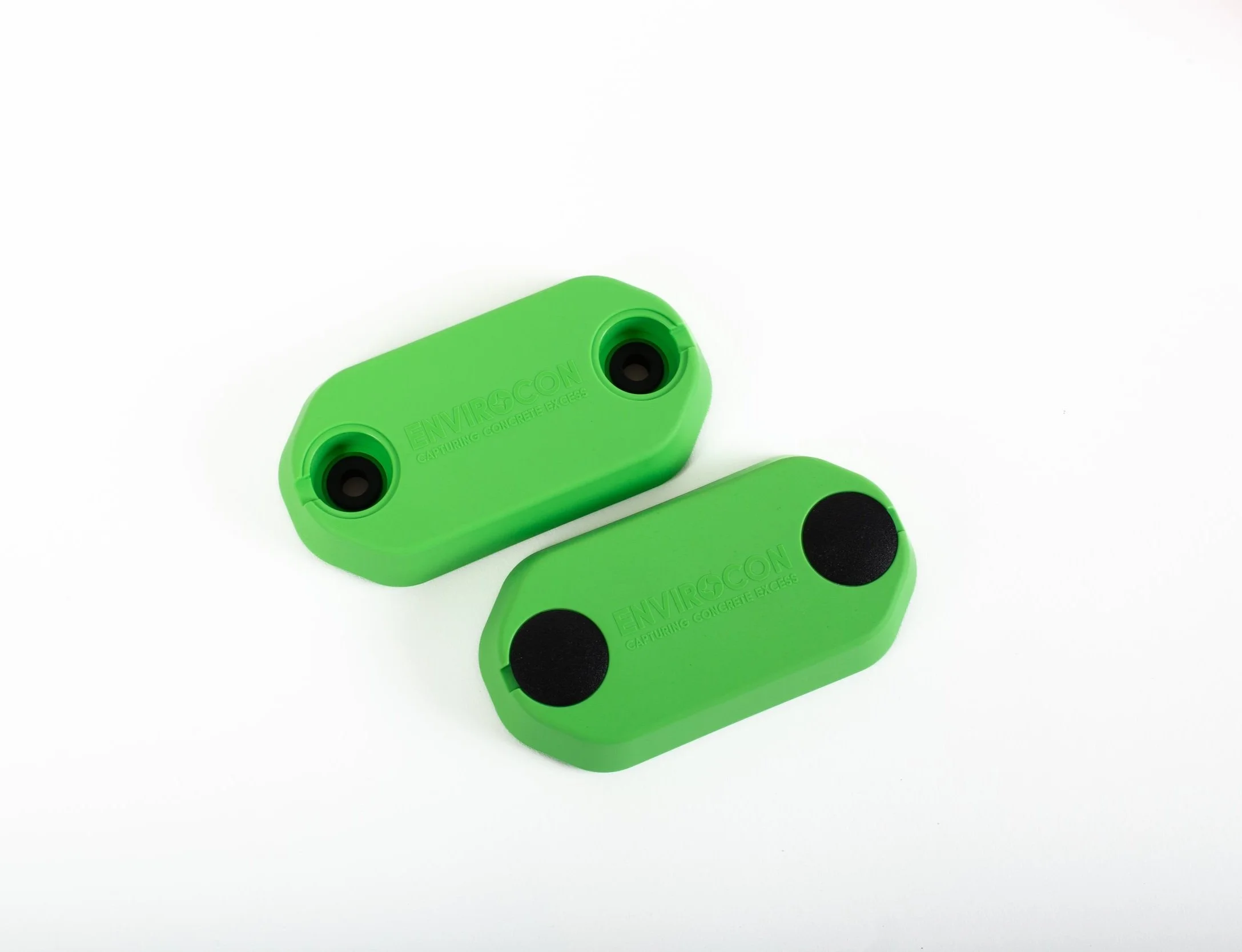
